Lab managers have a lot on their plates, from managing staff, to workflows, to purchasing and maintaining equipment. One thing that puts a wrinkle in any lab manager’s day is malfunctioning machines. A broken instrument can hold up processing samples, increase the time it takes to get results, idle workers, and create a lot of friction “from above.”
Here are seven key tips to help you keep your equipment running well from Evolve’s perspective working with hundreds of great labs over the last 20 years.
1. Read the operator’s manual
Getting people to read the operator’s manual is a challenge. Most operator’s manuals are not very technical. They are geared towards the end user, so don’t be intimidated. Also, the trouble-shooting section of each manual is invaluable. You can often use it to help identify simple problems you can likely fix yourself.
If you can’t find a particular operator’s manual, you may have luck locating it online with a simple Google search. If not, contact the machine’s manufacturer or see if the service company that maintains your equipment can get you one. If you don’t have one already, we highly recommend starting a library of operator’s manuals on all the equipment in your labs.
2. Get proper training
Depending on the size of your lab and number of people working for you, consider having one or more staff members get factory training at the time you purchase a piece of equipment. This gives them and your lab the tools you’ll need to properly operate the unit, perform basic troubleshooting, and have an overall comfort with the instrument. For older units, it might be worthwhile to get an operational training class from Evolve.
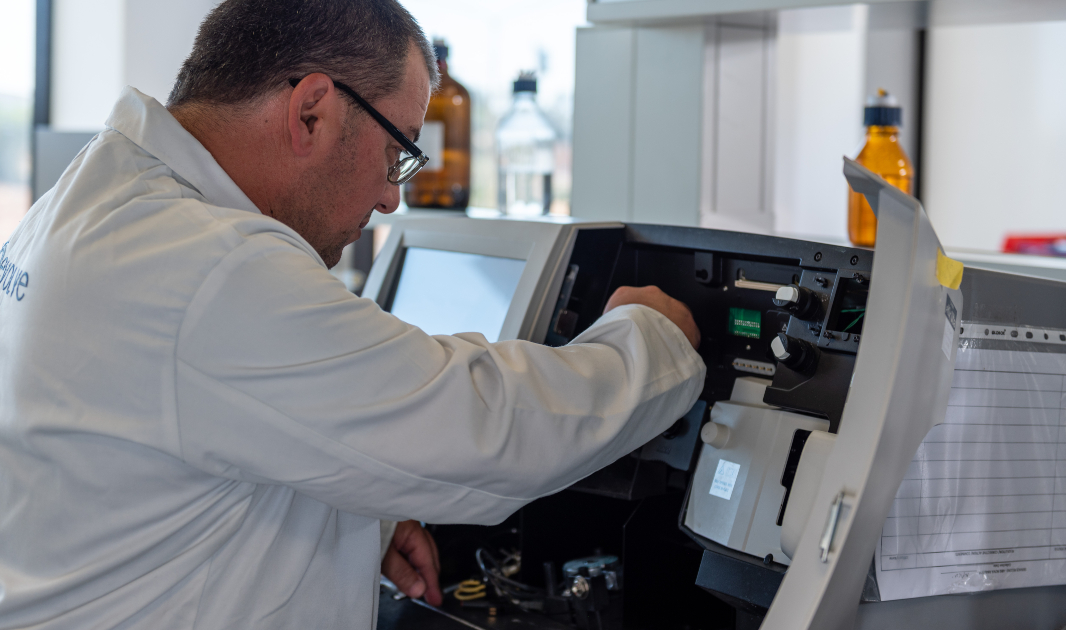
3. Conduct daily maintenance
“If it looks good, it works good.” Keeping a machine clean will help keep it operating smoothly. Create and adhere to daily, weekly, and monthly schedules for routine cleaning and maintenance. As an added bonus, doing this will help you to become “one with the machine.” You’ll start noticing small changes that could indicate a problem, such as fluid in the bottle being lower than the previous week.
Part of a good maintenance routine should include spending a few minutes at the end of each day cleaning up broken glass, spilled reagents, etc. Doing this will help keep messes from migrating into other areas they don’t belong and possibly negatively impacting other machines. Good maintenance should also include keeping a logbook for each unit in the lab. Note everything possible that happens with the unit, including: temperatures, fluid changes, waste dumps, and errors. Your logbook will help the manufacturer or service personnel accurately troubleshoot when you have an issue. You can never have too much information, especially when you have multiple people using your instruments.
4. Trust, but verify
Sales reps are very nice people, but often they are not technical reps. When in doubt, call the manufacturer with your technical questions. If your issue involves service, call the team of engineers at Evolve. They have been trained to know your instruments inside and out.
5. Look for warning signs
Prevent something major from happening by addressing it early. It doesn’t mean you have to panic, but be mindful. Sometimes issues show themselves with subtle (but very helpful) clues, early on. As I said in the daily maintenance section above, become one with your machine. If something looks a little “off,” don’t ignore it. Explore and address it early on. Look at your manual. Or call your service tech to get insights and help asap. It may be something that only takes five minutes to fix. And addressing it right away might save you five days of down time later. Your service tech could also offer phone support that quickly resolves the issue without an onsite visit.
Again, this is where an equipment log comes in very handy. Something as simple as lights flickering in the lab can cause issues with extremely sensitive electronics. A few drops of fluid could be an indication that an O-ring seal is going bad. Be mindful of slight changes.
6. Have preventive maintenance done every year
Not only is your equipment something you depend on every day, but it’s expensive. The best way to extend its life is to do a thorough inspection and cleaning every year. Replace any parts that need it. You’ll stay on top of issues and avoid costly downtime by doing this.
7. Build a well-stocked toolbox
Say you start your shift to find a machine is not working properly. You call the OEM or your service tech for help. They assure you, the machine just needs an easy fix. They say, “All you need to do is get a 4-mm Allen key and a #1 Phillips head screwdriver, do a couple of things we’ll guide you through, and we’ll have you up and running in no time.” You see where this is going…If you don’t have a good set of tools, you may be in for some totally unnecessary downtime—whether it be hours or an entire day until your tech can arrive onsite.
Put together an organized box of basic hand tools and know how to use them. Remember, you often get what you pay for, and that’s especially true with tools. Quality tools will last a long time, if used properly. Be sure to invest. A few hundred bucks should more than cover it.
“What tools do I need?” you ask. Here’s my recommended list:
- Slotted and Phillips head screwdrivers of different sizes
- Set of Allen wrenches, both metric and American standard
- Needle-nose and standard pliers
- Forceps
- Toothbrush
- Oil or grease / Super Lube (be sure it’s the correct kind for a given machine)
- Duct tape
By following these tips, you can ensure your lab and equipment will run more efficiently. You’ll also have less down time, avoid a lot of frustration, and save money.
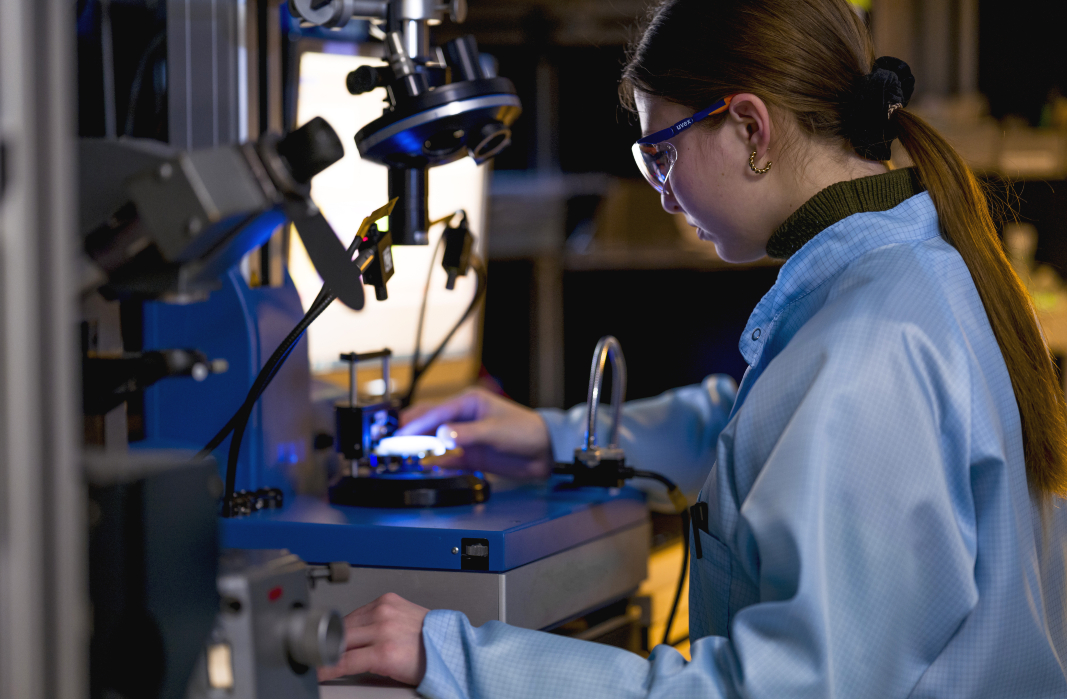
You might also be interested in
Industry insights, innovative ideas and exciting announcements from Evolve
What can Evolve do for you?
However big or small your business or organisation, we can make life easier.
Our specialists have all the skills needed to allow your new science laboratory project to thrive. From initial design, supply and installation of furniture to providing all associated building services, Evolve has the in-house expertise to deliver on time and within budget. We can help you determine the best way to make use of your available space while prioritising safety, space, and accessibility.
Evolve has supplied and fitted lab furniture and accessories to a range of companies and institutions over the years.
We also offer a range of additional services, including fume management, network cabling, electricity distribution and testing, plumbing and testing both for water and gases as well as all drains and speciality gases.
We’re ready to be by your side to help you design, equip and maintain a fully EU-compliant lab for your next project. For a complete, professionally-delivered project from initial design through to completion, get in touch with Evolve today.
Hassle-free maintenance from Evolve
Technical support is a core element of the service we provide to all Evolve customers, from a small laboratory with a single bench, to a major healthcare or industrial organisation with multiple systems, or a complex, high-volume water purification plant.
Our customer support services include system design and build, installation and commissioning, as well as long-term maintenance contracts to optimise efficiency and minimise through-life costs.
Evolve’s team of experienced engineers, based in Malta, can also provide dedicated support, including consultancy, trouble-shooting and product training.